Lean Six Sigma Consulting in New Jersey
Contact Us
The Lean Six Sigma Process
When a company creates a product or service, Lean Six Sigma Experts of New Jersey is the company to call when looking to eliminate irregularities, service faults, or defects. Lean Six Sigma, in general, employs a control map of elements that correspond to the commodity production process. When converted into the points on the table, the approved goods and procedures must fall into a certain group. Additionally, points that are outside of the defined limits are called system faults.
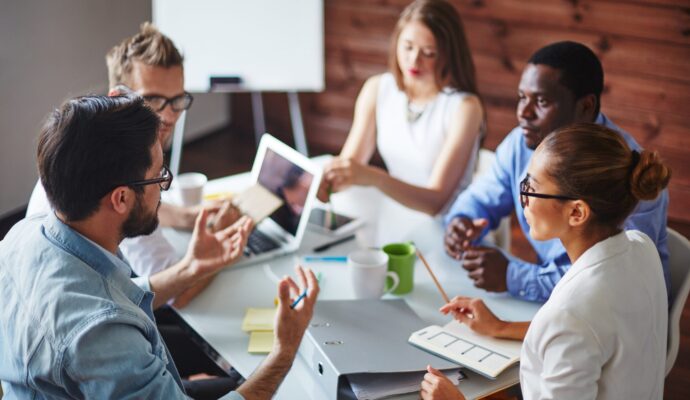
Reasons to use Lean Six Sigma in New Jersey
- Help you build your business strategy: Lean Six Sigma is critical to a company’s success. When a company decides on its work, goals, and performs SWOT analysis, using Six Sigma approaches allows you to focus more accurately and efficiently on places to improve. If Lean Six Sigma is to become a market leader, it must improve its efficiency, boost its internal processes, maintain the lowest-cost suppliers, and prevent unnecessary problems.
- Maintains motivation of employers and employees: Entrepreneurs and business owners constantly forget the efficiency is dependent on employers and staff. This contributes to improved efficiency, which leads to increased service revenue. However, employees must be motivated and encouraged to function and succeed daily. Companies that keep their employees involved have a 25 percent to 50 percent rise in inefficiency. Implementing Six Sigma problem-solving methods and tools effectively promotes career growth and contributes to the establishment of a balanced organizational culture of information exchange and employee engagement.
- Help you to reduce cycle times dramatically: Companies often miss deadlines. This is largely due to improvements in the project’s complexity and recent management policy changes. You will shape expert teams all over the company utilizing Lean Six Sigma approaches. Professionals with a variety of technical areas are often sought. This unit examines the conditions that might jeopardize the project’s long-term success. The team would then be forced to identify solutions to mitigate the potential consequences. A 35 percent reduction in cycle times has been announced by several prestigious Six Sigma firms.
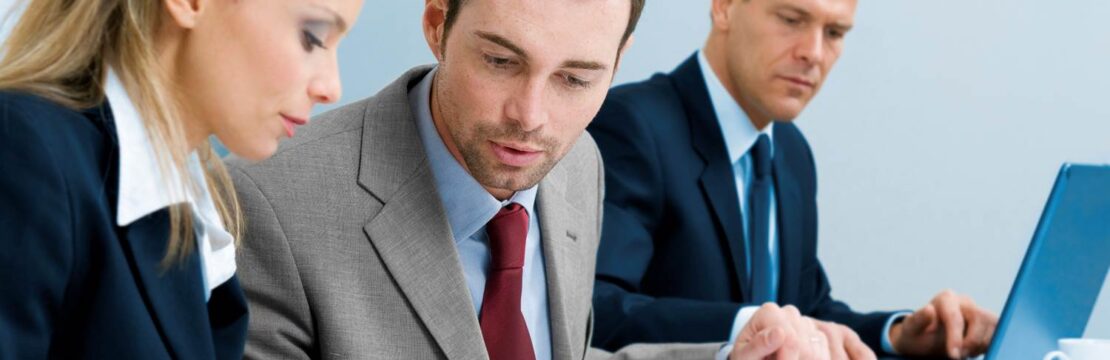
FAQ’s
Given that it appears that increasing expertise is needed to capture certain commonly asked questions when assessing prospective partners while selecting the right Lean Six Sigma partner is all that is required for program growth, the option of any additional partner, provider, or supplier is critical. Some of the questions below will give you an indication of the kinds of responses to expect:
With you and other main stakeholders in the company, a company like Lean Six Sigma Experts of New Jersey can cooperate and form a cross-functional execution team. You can choose a partner that is knowledgeable about coaching, tactics, and best practices. Participants may have realistic experience using any of the current process control methods to achieve business outcomes as well as an understanding of the overall company policy and consumer approach. This could raise a red flag if you just have instruction during the first stage of the startup process. An awareness of the consumer strategy and current evolving management and process change cultures can be the starting point for every Lean Six Sigma implementation at an organization, supplemented by a roadmap that adapts the approach to certain realities. When Lean Six Sigma is implemented into a company's ecosystem, project selection is important. One of the most important facets of this process is the division of conceptual priority areas into concept proposals. The project acquisition process can ensure that high-value, well-established ventures are identified and connected to strategic priorities, minimizing project lead times and internal corporate capital shortages. Following the identification of proposals, a meeting with key stakeholders should be held to confirm timely conclusions and prioritize programs. There are not only several Lean Six Sigma systems to be found, but also other activities to be addressed. The startup process should be seen as a project charter for chosen Lean Six Sigma project plans, including the company case for each project. We're also establishing baseline criteria at this stage, which will enable us to monitor process efficiency and changes. It is important to use the methodology consistently over time; the team must be mindful of its roles and commitments. Each member of the team must be evaluated objectively to achieve the team's goals. Similarly, in the company, Lean Six Sigma should be seen as a long-term approach rather than a series of steps; everything has to be improved. Management's approach to the plan paves the way for the future; tradition and approach are most important than a company. Long-term dedication is needed; the approach must be reflected in the policies and operational framework. To assess results, present and use facts and statistics; recognize compliant behavior in corporate culture. It's important to recognize and reward the latest accomplishments. Several people inform us, "We are a customer-driven company!" Sounds great, so what distinguishes conventional companies from customer-centric businesses? Customer-driven companies, on the other hand, are committed to providing high-quality goods and services that satisfy the demands of their clients. Lean Six Sigma Experts of New Jersey offers resources and a framework for defining and measuring consumer requirements. "What Success Looks Like" is now free of doubt. Can you recall the statement that "bad systems cause 95% of errors"? In certain organizations, errors are labeled as "a people matter" or "a human mistake." They use faulty systems to attempt to fix people. A Lean Six Sigma environment focuses on manufacturing productivity and Lean systems. To minimize failures, efforts are being made to improve systems. Human presence in repetitive jobs can be eliminated or automated. This eliminates the monotony of routine jobs and frees up workers' ability to focus on higher-value activities. Individuals may learn a variety of strategies regularly. Since applying the strategies and implementation inside their organizations, they would be willing to educate everyone about them; all of this contributes to professional growth.
What is your new customer start-up process?
What are the selection and setup procedures for your project?
Is Lean Six Sigma a sequence of initiatives for improvement?
How does the customer benefit?
How do workers benefit?
There are so many areas or regions where we offer these services with most of them being cities.
However, if you need any of these services, you need to contact us. The list below comprises the areas where we offer these services.